The History and Advancements of Woodworking Machinery
In ancient times, carpenters relied solely on hand tools to form and mould wooden objects, dating back centuries to the earliest civilisations. However, with the advent of the lathe in ancient Egypt, woodworking became a more efficient craft. Followed by early forms of woodworking machinery such as drills, saws, and chisels, a vast array of innovative woodworking machinery emerged in the 19th century. Planing machines, circular saws, mortising machines, and shapers revolutionised the woodworking industry, boosting production, efficiency, and accessibility, enabling the craft to reach a broader market.
In contemporary society, woodworking machinery from companies such as elitewoodworkingmachinery.ie showcases advanced automation and high-tech features such as laser cutters and Computer Numerical Control (CNC) routers. The evolution of woodworking machinery highlights a rapid climb from the craftsman’s hand tools to the intricate and high-precision technology of the CNC router.
Types of Woodworking Machinery and Their Functions
Woodworking machinery exhibits a range of specific functions, and individual machines address each woodworking technique. This range includes:
- Table Saw: The most widely used woodworking machinery globally, utilised for cross-cutting, ripping, and bevel cutting in materials. It comprises a table with an underneath-mounted blade that slices through the wooden material as it is pushed through the apparatus.
- Band Saw: A continuous long blade with teeth to cut thin stock, useful for curved cuts, resawing, and ripping thin material.
- Jointer: It serves to flatten and create squared board faces. The machine has an infeed and outfeed table, aided by a cutter head that removes material between them.
- Thickness Planer: Woodworkers use this machinery to level the material board’s thickness uniformly. It consists of an infeed, an outfeed table, and a cutter head that removes excess in between the tables.
- Router: A versatile woodworking machinery that employees use to create decorative edges, cut mortises, dovetails, box joints, and more. It has a spinning bit adjusted to cut at different depths and angles.
- CNC Router: It comprises a computer-controlled router used for a precise cutting capability to create complex shapes and intricate designs with ease.
Efficiency and Production of Woodworking Machinery
The output, efficiency, and productivity levels of woodworking machinery correlate with the specific machinery and its capabilities. In general, more technologically advanced machinery tends to have higher output rates and exhibit higher efficiency, while the simplest ones require more time and effort to achieve the same results.
For instance, a CNC router makes intricate, amplified designs within a fraction of the time required to carve designs manually. However, a traditional hand saw is sufficient for small-scale woodworking projects, particularly for craftsmen who prefer to use hand tools.
Features and Capabilities of the Best Woodworking Machinery
The best woodworking machinery has advanced features that optimise productivity, efficiency, and output rates. The unique features include:
- Automation: Modern machinery implodes automation, diminishing time consumption and exertion during operations.
- Duct Collection: Dust Collection Systems play a central role in woodworking. They remove sawdust and debris from the workspace, eliminating possible hazards.
- Safety Features: Innovations such as automatic shutoffs, blade brakes, and guards in machinery minimise the risk of accidents and injuries.
- Precision: Advanced woodworking machinery is equipped with digital readouts, lasers, and other high-precision tools to ensure accuracy and consistency in results.
Tips for Selecting the Best Woodworking Machinery
While selecting woodworking machinery, project requirements, among other factors, must be taken into account. These factors include:
- Project Type: The type of woodworking project determines the necessary machinery required. For instance, CNC routers create intricate designs unachievable through traditional saws.
- Budget: Cost is a significant factor to consider while selecting woodworking machinery. Advanced machinery tends to cost more but provides greater output and efficiency.
- Space: The machine requirements dictate the workspace. Larger machinery requires more space, making it necessary to consider the available workspace when selecting the machine.
- Experience: Mastering the art of woodworking calls for not just a keen eye for materials and designs but also a profound knowledge of the latest technological advancements in machinery.
The evolution of woodworking equipment has undergone a drastic transformation since its inception, marked by an influx of cutting-edge features, advanced precision tools, and automation. In contemporary times, the selection of appropriate machinery has become the backbone of enhancing productivity, efficiency, and guaranteeing adequate safety measures. In the able hands of an accomplished artisan, the infusion of sophisticated machinery translates to the creation of impeccably detailed woodwork designs.
The timeless essence of traditional woodworking endures as a testament to the unerring human skill, dexterity, and artistry that characterises this learned craft. From vintage handheld tools to the latest Computer Numerical Control (CNC) routers, every element of woodwork demands a high degree of dedication, mastery, and patience.
In essence, the key to achieving optimal woodwork design outcomes hinges on several elements. Foremost, the comprehensive mastery of intricately fashioned machinery, the deliberate selection of appropriate tools and equipment, and a rooted appreciation of the craft and its unerring artistic process are fundamental. This indispensable approach guarantees an uninterrupted love affair with the process of crafting bespoke woodwork pieces.
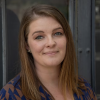
Lynn Martelli is an editor at Readability. She received her MFA in Creative Writing from Antioch University and has worked as an editor for over 10 years. Lynn has edited a wide variety of books, including fiction, non-fiction, memoirs, and more. In her free time, Lynn enjoys reading, writing, and spending time with her family and friends.