There’s a strange quiet that settles over a job site after an accident. Machines go silent. Radios stop buzzing. People stand still, unsure whether to look or look away. And even though construction workers are some of the toughest people out there, no one walks away from that kind of moment untouched. That’s the part people outside the industry never really understand. They see the hard hats and the gear, but not the human cost when things go sideways. Safety isn’t just a line item or a checklist. It’s the difference between making it home at the end of the day or not.
And still, day after day, there’s pressure. Get it done faster. Trim the fat. Skip the boring stuff. But the boring stuff—those safety briefings, those refresher courses, those spot checks—are the only things standing between routine and disaster. If you’ve ever asked yourself where safety really fits into the bigger picture, or whether it’s being done right on your job site, you’re not alone. Let’s take a look at where things are falling short, and what can actually be done about it before the next siren goes off.
Training Isn’t the Problem—Until It Totally Is
Most crews know the basics. Hard hats. Harnesses. Watch your footing. Don’t stand under a suspended load. It’s not about ignorance; it’s about repetition. The truth is, people get too used to the job. They stop noticing small hazards because they’ve walked that same path a thousand times and never tripped. But that’s the moment risk creeps in—when the abnormal starts to feel normal.
Managers and supervisors often assume a toolbox talk here and there will cut it. But without ongoing, structured safety education, things start to slip. That’s why more construction companies are rethinking how they approach certification. Not just for the sake of compliance, but because real training saves lives. And now, it doesn’t require hauling everyone off-site or losing a full day’s productivity. Programs like CHST certification online are changing the game. They give team leaders the tools they need to build safety into the culture, not just tack it on at the end of a long shift. Online certification means faster access, less downtime, and a clearer sense of ownership—without feeling like a chore.
When safety becomes an afterthought, people get hurt. And when training becomes part of the everyday language, the whole site runs smoother. The trick is making it feel like a skill upgrade, not a punishment.
The Trouble with Shortcuts No One Talks About
If you’ve ever cut a corner to save five minutes, you’re not alone. Everyone has. You tell yourself it’s just this once. You think, “I’ve done this before. I know what I’m doing.” Then one day, that ladder wobbles just wrong, or that old cord sparks unexpectedly, and suddenly you’re one of the stories they tell in training sessions.
Shortcuts have a cost. Maybe not right away, but eventually. And it’s not just personal risk—it’s morale. When workers see that safety is being pushed aside, even quietly, they start to question who’s really got their back. There’s this unspoken pressure in construction to act tough, keep your mouth shut, and not slow the team down. But silence is expensive. It leads to injuries, lawsuits, and that hollow feeling when a guy doesn’t show up for work because he’s in the hospital.
The answer isn’t more rules. It’s buy-in. People need to see that safety isn’t just about avoiding fines—it’s about showing up for each other. Creating that kind of environment doesn’t take fancy systems. It takes consistency, accountability, and leadership that walks the talk.
When Planning Is Poor, Accidents Happen
No one likes paperwork. No one gets excited about reading floor plans or marking off zones with tape. But when job sites skip over careful planning, hazards multiply. From faulty scaffolding setups to unclear equipment schedules, accidents often start on the whiteboard. And nowhere is that more apparent than in poor traffic control. One truck going the wrong way, one distracted operator near a pedestrian area—that’s all it takes.
People assume these mistakes only happen when someone’s brand new, but veterans slip up too. Fatigue, assumptions, bad communication—these all add up. What helps is building plans that aren’t just for show. Real, living schedules. Clear signage. Meetings where questions actually get answered instead of brushed off. When foremen know they have the authority to pause a job and reroute something that isn’t safe, you’re going to see fewer close calls.
Safety planning isn’t something you check off at the beginning and forget. It has to evolve every single day, just like the site does.
Weather, Fatigue, and That ‘Push Through It’ Culture
One of the more invisible dangers on a site isn’t something you can measure. It’s the pressure to keep going when your body is screaming for a break. Maybe it’s a 95-degree day and you’ve already had to take off your vest twice just to breathe. Maybe it’s been raining for three straight hours and your gloves are so soaked you can barely grip your tools. Or maybe it’s week six of working Saturdays and you’re trying to focus while your eyelids keep dropping.
Fatigue, dehydration, and stress slow down reaction time and cloud judgment. Everyone knows it, but the culture doesn’t always allow space for recovery. There’s pride in pushing through, in not complaining. But people aren’t machines. And the more leaders start acknowledging that out loud—by adjusting timelines when weather hits, or rotating crews before burnout sets in—the better the work will be. Safety doesn’t mean going slower; it means working smarter. And often, that starts by actually listening to the people doing the heavy lifting.
How Small Daily Habits Stack Up
Safety isn’t always dramatic. It’s usually invisible. It’s the guy who checks the ladder before every climb, even though no one told him to. It’s the new hire who asks a question instead of pretending he already knows. It’s the foreman who walks the perimeter each morning, not because he has to, but because he cares.
Those little things add up. And the teams that get it right don’t rely on luck or paperwork. They rely on each other. It’s not about perfection. It’s about awareness. And when people feel like their safety matters more than the schedule, they work better, faster, and with more loyalty.
Wrap-Up
The construction industry isn’t soft. It’s not made for people who cut and run. But if it wants to thrive, not just survive, safety has to stop being treated like a side note. It’s not an expense. It’s an investment—in people, in families, and in the kind of jobs everyone can be proud of.
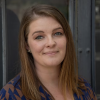
Lynn Martelli is an editor at Readability. She received her MFA in Creative Writing from Antioch University and has worked as an editor for over 10 years. Lynn has edited a wide variety of books, including fiction, non-fiction, memoirs, and more. In her free time, Lynn enjoys reading, writing, and spending time with her family and friends.