Efficiency is important within the fast-paced world of logistics that exists nowadays. Warehouses operate to reduce mistakes, maximize efficiency, and obtain actual-time inventory information. RFID warehouse management technology has come to be helpful in this situation and has furnished a robust solution.
RFID routinely acknowledges and tracks tagged goods using radio waves. Unlike conventional barcodes, which have to be scanned in line of sight, RFID tags may be studied remotely—even through items like boxes or bins. This will increase performance and lower human errors through allowing faster and greater stock management.
Why Choose RFID for Warehouse Management?
RFID has numerous advantages over traditional barcode systems for warehouse management.
Improved Accuracy: Automatic statistics seize eliminates manual scanning mistakes and guarantees real-time stock statistics.
Improved Visibility: Monitor the stock drift from receiving to picking and delivery throughout the warehouse.
Enhanced Productivity: Using faster information gathering methods, simplify tactics which include picking, packaging, and cycle counting.
Reduced Labor Costs: Automate mundane tasks and decrease reliance on manual labor for stock management.
Better Decision Making: Prevent stockouts, maximize ordering, and accumulate real-time insights into inventory levels.
Advice on RFID Installation in Your Warehouse: A Complete Guide
When implementing an RFID system in your warehouse, planning and organization are necessary. Below is a summary of the essential steps:
1. Assess Your Needs
Determine your pain points: Analyze your present warehousing procedures first. What difficulties are you having? Do stock differences occur frequently? Does cycle counting take a lot of time?
Establish objectives: Clearly state your goals for using RFID. Do you want to see your inventory in real-time, cut down on shrinkage, or increase picking accuracy?
Think about ERP versus WMS: Analyze the software infrastructure you currently have. A warehouse management system (WMS) is specific to warehouse operations, while a corporation’s applicable resource-making plans (ERP) gadget oversees all corporate responsibilities. Assess whether you combine RFID with your ERP or want a separate WMS with built-in RFID abilities.
2. Site Survey and Planning
Warehouse layout: To ascertain the precise arrangement of your warehouse, carry out a comprehensive site study. This involves locating potential barriers to transmitting RFID signals, such as metal shelving or areas with significant humidity.
Choose a tag: Based on the type of inventory you have and your budget, select the suitable RFID tags. Think about things like durability, read range, and size. Tags come in three primary varieties: semi-passive, which has a small battery for an extended read range; passive, which depends on reader power; and active, which has a battery and may send out its signal.
Placement of the reader: Deliberately arrange RFID readers across the warehouse to guarantee that your selected tracking zones are fully covered. Dock doors, choosing zones, and entry/exit points may be examples.
3. System Integration and Testing
Software Integration: For centralized data management, select RFID software that works in unison with your current WMS or ERP. The software must automatically update your inventory system, decode data from RFID tags, and capture the tag data.
System Testing: To guarantee precise tag readings and seamless software integration, thoroughly test the complete RFID system. This assists in locating any possible problems before full deployment.
4. Staff Training and Deployment
Employee Instruction: Train your warehouse workers to use and operate the new RFID technology. This involves being aware of the many kinds of tags, how readers work, and the best ways to handle inventory that has been RFID-tagged.
Implementation and Observation: Deploy the RFID system gradually, beginning with a pilot project in a designated region. Keep an eye on the system’s functioning and make any necessary modifications.
Conclusion
Putting an RFID system into place calls for planning. Through meticulous assessment of your requirements, strategic deployment planning, and employee training, you can harness the potential of RFID solutions to enhance warehouse operations. The advantages extend beyond quicker cycle counting and better picking accuracy. Real-time access to inventory enables data-driven decision-making, improving forecasting, lowering carrying costs, and ultimately creating a more productive and profitable warehouse.
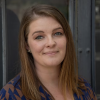
Lynn Martelli is an editor at Readability. She received her MFA in Creative Writing from Antioch University and has worked as an editor for over 10 years. Lynn has edited a wide variety of books, including fiction, non-fiction, memoirs, and more. In her free time, Lynn enjoys reading, writing, and spending time with her family and friends.