The manual labor industry is huge here in the U.S. and is responsible for the development of every town and city in the country. From creating new office blocks to ensuring homes meet regulations, this sector truly is the backbone of our nation.
Our reliance on manual labor means industries like construction have plenty of workers and they’re worth a lot of money. According to recent data, there are over eight million construction workers currently employed and is worth around $2.3 trillion.
Sectors that require manual labor work are constantly looking for better working practices to ensure standards continue to be met while improving efficiency. This should lead to happier clients and more money to be made for individual firms across the country.
With that in mind, manual labor will continue to evolve in the future and our article is going to take a look at some of the main ways this may happen. Continue reading to see what the future holds for manual labor here in the U.S.
Why is improving manual labor necessary?
Before looking at the future trends in manual labor, we thought we’d highlight why it’s necessary to continue evolving an industry that already works so well. Here are some of the main reasons why it should be done:
- It can boost productivity
- You can gain a competitive advantage
- Enhanced customer satisfaction
- Staff members will be safer while working
- It can make your business more sustainable, helping to support environmental initiatives
How will manual labor change in the future?
Technology and automation
Automation is something that many sectors are looking at and it won’t be long until we see this in manual labor work too. By automating processes, businesses can save time and money, while cutting out human error. Some things that may be automated in the future include bricklaying, self-driving bulldozers and 3D-printed products that would’ve once been made by a human.
The downside to this is that it may impact the employment rate with robots able to replace physical workers for a fraction of the cost.
Better tools available
There will be better tools available from reputable suppliers like RS Americas. Technological advancements mean power tools, for example, are more powerful, long-lasting and have better runtimes. This should help manual laborers work more efficiently and improve the quality of the work they’re producing for clients.
Addressing skill gaps and training needs
Training and development are important for all sectors as they can improve the standard of work and maintain health and safety expectations. There is a skill gap in some areas of manual labor in this country and better training opportunities may help to address that. This should result in a better workforce.
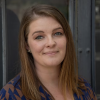
Lynn Martelli is an editor at Readability. She received her MFA in Creative Writing from Antioch University and has worked as an editor for over 10 years. Lynn has edited a wide variety of books, including fiction, non-fiction, memoirs, and more. In her free time, Lynn enjoys reading, writing, and spending time with her family and friends.